Produce sorting equipment data useful from processing line back to the field
Although sorting equipment is capable of collecting an incredible amount of data, most of that data goes unused. But that data can be extremely valuable, which is why sorting equipment manufacturers, like Key Technology, TOMRA and Newtec, are helping customers use it to improve production, efficiency and quality both up- and downstream.
Key looks beyond safety and quality
For the most part, processors have used sorting equipment to improve safety and safeguard quality. Now, though, they’re using it to optimize their line, going even as far as the farmer, said Karel Van Velthoven, Advanced Inspection Systems Product Marketing Manager, Key Technology.
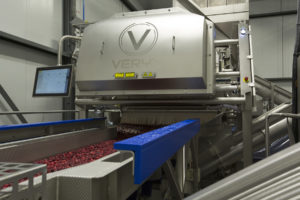
Key Technology’s most advanced sorter, VERYX, has been equipped with Information Analytics to do just that. VERYX is a digital sorting platform with both belt-fed and chute-fed models in different widths.
“One huge side benefit of using a digital sorter comes from leveraging the technology as a data center,” said Van Velthoven. “When equipped with an ‘Information Analytics’ capability, a sorter can collect and analyze big data to reveal patterns, trends and associations that can be acted on to enhance operations.”
In one case, a VERYX user asked Key Technology to create an advanced analytics package to analyze its leaf-to-stem ratio in spinach.
“The end-goals include optimizing raw material utilization to increase yields, improving line efficiencies to reduce costs and eliminating product quality and food safety problems,” said Van Velthoven.
Sorting equipment can also be used to do predictive maintenance on other equipment. For example, a walnut processor uses data from VERYX to quickly determine when equipment is malfunctioning earlier in the line. Walnuts are a high-value product, said Van Velthoven. Being able to quickly assess when the cracker is damaging good kernels saves the customer in yield loss.
Vincent Godin, president of Emblème Canneberge, said they use Information Analytics to extract product and operational data that helps improve processes, including field production.
“By monitoring the number of ejections for each type of defect, we learn about the quality of incoming product,” he said. “If we see too many white or yellow berries, we can let that grower know and suggest that they add sulfur to their field a little earlier next year.”
Key Technology recently acquired Herbert Solutions, a company that also makes sorting equipment. Designed with 360-degree vision, Oculus inspects whole potatoes using infrared cameras to identify green spots, and digital color cameras to identify defects. Oculus also sorts to grade, removing potatoes afflicted with bumps and notches, skin discoloration, and common defects such as mechanical damage, common scab, cracks and black dot. While removal of foreign material is not its main function, it does remove some. Anything that doesn’t look like a potato can be targeted. Next to the above, it also sorts on size and can do so in three grades. This ensures potatoes are sent to the correct processing line, which avoids yield loss.
Using Oculus and VERYX in combination offers further advantages in terms of efficiency both upstream and downstream, said Van Velthoven. Reviewing quality further up the line, for example, can tell you if there’s something wrong earlier in the line.
“If the sorter sees a lot of peel passing by then eventually you know something is wrong with your peeler,” he said. “If your cuts are wrong, then something is wrong with your cutter. Being able to link that back upstream and also downstream, that’s very valuable information in terms of efficiency.”
TOMRA Insight offers improved efficiency
Norwegian company TOMRA Sorting Solutions also offers advantages beyond the equipment’s main task. Let’s look at TOMRA 3A, a robust optical sorter that uses near infrared (NIR) multi-spectral sensors to examine product in flight to differentiate between potatoes and foreign material. Color sensors detect unwanted green potatoes and remove foreign material such as stones, soil clods, rocks, wood, bone, plastic, glass, metal and rubber. Beyond that, though, customers want to utilize data generated by their sorting equipment to make further improvements. As the head of Digital at TOMRA Sorting Solutions, this is Felix Flemming’s responsibility.
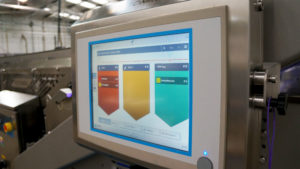
TOMRA Insight, he said, collects two types of data. The first is health data on the machine itself, which can help predict maintenance more quickly and reduce downtime. The second type of data is product data, mostly around quality.
Beyond that, there are two other areas where you can create value from data, said Flemming. Data can also determine the throughput of the machine by looking at product distribution across the belt to improve yield. “If you get 1 percent improvement on your yield or on your throughput that could translate into more product and more revenue,” said Flemming.
Data can also be used to reduce operational costs by providing service reports and document management. But the biggest benefits come from defect data, said Flemming. Processors, for instance, can compare defect reports between the different supplier farms. Together, they can use the data to assess whether or not on-farm management practices, such as pest management or fertilization, are working. The same data can provide more information on how product fared in storage.
“You can really make fact-based decisions in the end,” he said. “It’s no longer just a gut feeling.”
Newtec WebServices enhances traceability
Based in Denmark, Newtec manufactures weighing, packing and sorting equipment. Celox-P-UHD, for instance, is an optical sorting machine that grades potatoes based on size, shape and quality. It can deliver product in up to 14 different categories. When coupled with Newtec’s internet-based business information and productivity tool, WebServices, processors can collect, analyze and present relevant production data, including alarm systems, downtime reports, statistics on production and products, and details, such as size, distribution, quality and waste. Access to this type of data not only improves efficiency, but also traceability, explained James Antony, Newtec software developer.
Antony pointed to the sorting of potatoes as an example. Rate of rejection could be due to faulty product, but it could also be due to human error, he said. WebServices can also analyze the speed at which product is fed versus what it can actually handle. Using the software, processors can create alerts via email or SMS to improve response times.
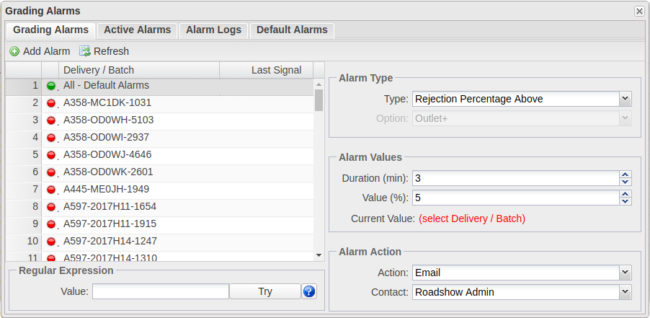
Data from WebServices can also be used to assess quality issues. In one case, a farmer had delivered batches of highly damaged carrots. Once alerted to the problem, the processor was able to contact the grower. It turned out the farmers new harvesting equipment had not been properly calibrated. They were able to address the problem before too much damage was done.
Data analysis could be used to determine insect damage, or quality issues due to maturity or fertilization.
At this point, WebServices can only provide a static report, but Antony hopes to be able to automate the information in the near future. Their goal is to be able to provide customers with analysis, as well as recommended action. This information could help to reduce bottlenecks and cut losses more quickly. Ultimately, their goal is to automate the entire line using sorting data to prepare further downstream in the weighing and packing sections.
(Top photo — A TOMRA 5A sorter in action during potato sorting.)