The new labor
As the labor market continues to rebound from pandemic-related shortages, CPGs are focusing their workforce on key growth areas as they try to meet continued high consumer demand for food and beverage products.
Workforce shortages and supply chain instability are reducing operational efficiency and margins. Job openings — at more than twice the gap to reach pre-pandemic employment levels — are near all-time highs at more than 800,000. Sourcing bottlenecks and global logistic logjams are likely to remain challenges in 2022 along with cost pressure and inflation risk.
Ryan Womble, director of sales at Quest, a ProMach product brand, said that they have seen their customers struggling to hire and also retain. “In general, most of my customers are still reporting shortages, which is why we’re engaged in conversations with them regarding automation and specifically, from the packaging standpoint.”
Quest is a manufacturer of automation solutions, focusing on robotics and vision-guidance. The majority of Quest’s business is centered around produce and produce packaging with automation.
Dull, dirty and dangerous
Quest uses the term “Dull, dirty and dangerous” to indicate work that many people entering the workforce do not want to partake in, such as repetitive motion work. “They’re tough environments. It can be demanding work physically. And it’s challenging,” said Womble. “We spend a lot of time focusing, helping our customers to reduce the number of jobs that have those factors.”
Tasks such as sorting, pick and place and case packing can be monotonous, repetitive and sometimes dangerous. Automated equipment that performs these jobs has helped many manufacturers with the labor crunch, keeping humans performing duties that require a human’s touch.
Getting to the floor (or, crop) level, we also see repetitive, backbreaking jobs that can be done by a robot. As you will see in this month’s IFPA column on Page XX, Nexus has come out with a solution for a very basic and mundane task ― weeding. The company’s “robot as a service” approach allows companies to lease robots throughout their seasons instead of purchasing their own permanent fleet.
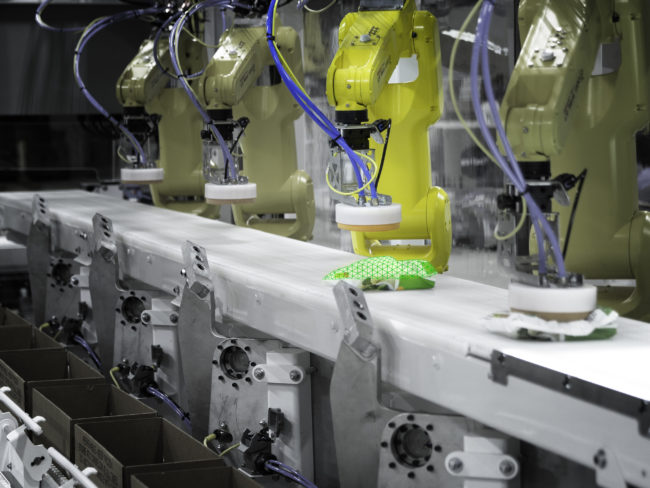
Training methods
Quest focuses a lot on training because they know their customers are going to have challenges. “They’re going to have different generations of people operating the equipment. They’re going to have a high turnover rate. So, we spend a lot of time making our equipment very easy to use. And most of that is driven from the main operator interface.”
It’s easy to get customer training from Quest. “(Our customers) have different generations of operating equipment. We spend a lot of time getting our equipment easy to use. The main interface is easy, things that require a mechanical adjustment,” explained Womble. “We want to eliminate as many of those manual changeover points as possible. And robots are a great way to do that. Robots give flexibility to adapt to different products and configurations. Again, using the flexibility of the robot versus a bunch of mechanical changeover points that you see in more traditional machinery.”
Quest has seen customers take on a variety of tactics to attract new talent, some of which are time-based incentives: By staying with the company over a period of time, employees will see specific and real incentives.
“Also, I do think training is a critical piece of that. Making workers the owner of their process and including them in the process improvement strategy is a big, big deal. I think it helps create ownership,” Womble said. Those people are living and working that role every day and they see opportunities to do things smarter and better than people at 10,000 feet don’t see,” Womble explains.
The real cost for their customers, especially in the produce industry, is fresh product has only hours of shelf life. “You measure that in an hour sometimes versus days and that time really matters. Lost production time typically significantly exceeds what you’re paying for from a labor standpoint to fix the problem,” said Womble.
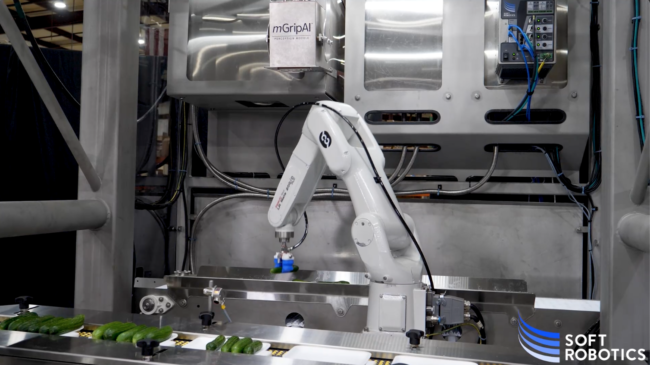
Generational gap
Womble said that they do see generational gaps. One generation is phasing out of the workplace and new employees aren’t fully trained. “Going to college was a big thing, now there is a gap in skills … we are maybe starting to correct that.”
According to Gallup, Gen Z and millennials now make up 46% of the full-time workforce in the U.S. There are four company traits millennials and Generation Z look for in an employer:
● The organization cares about employees’ well-being
● The leadership is ethical
● The organization is diverse/inclusive of all people
● Older millennials want open, transparent leaders
The bottom line? They want ESG — environmental, social and governance — in a workplace.
What’s next?
There’s already technology in the market, but Womble sees material handling equipment being widely adopted. AGVs, [automated guided vehicles] are not a new concept, but there’s a lot of new guidance and control technology out there that’s starting to become more full-fledged, just continuing to be developed. I think that’s probably the next big boom. And I think we’re right at the right at the bottom of that slope right now.
If you look at the traditional method for lift equipment, the labor, the cost of the equipment, and safety is probably one of the biggest impacts, Womble shared. “There are certainly collisions that happen. But one of the highest rates of injury in the workplace is people getting up and down off lift equipment. And then you have person to vehicle collisions. So, there’s labor, safety and efficiency.
Womble predicts that labor shortages will stay at about this level for the foreseeable future. “I think between the growth demand, especially around food production, the North American public is always going to be heavily focused on having their food and beverage products come from within our borders. Or at least on the continent significantly,” he said. Therefore, the labor will still be on North America.
Much of the manufacturing industry was already hurting for labor even before the pandemic; however, during the pandemic is when it was really magnified. Womble added that in the last 12 months, the industry has stayed at a high rate of unfilled jobs.