Digital platforms help power traceability, increase food safety
Despite industry efforts to maximize food safety, it’s not uncommon for produce to be associated with a recall related to cases of foodborne illnesses. In recent years, onions, romaine lettuce, sprouts and fresh salads have been recalled for this reason.
Recalls are expensive, potentially devastating to brand reputation and challenging to execute. It’s not easy to identify and locate affected product, especially if it was used as an ingredient.
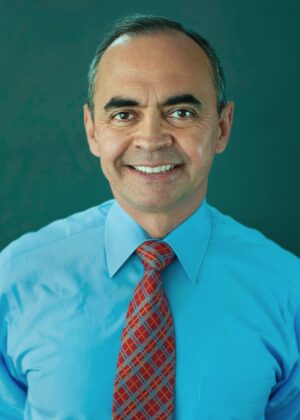
Digital technology can provide traceability and help pinpoint exactly which packages need to be recalled. With this technology, a QR (quick response) code or radio frequency identification tag provides each package with a unique identity. By scanning the code or tag, the stakeholder — e.g., wholesaler, retailer, consumer — learns about the origin of the product and whether that package needs to be recalled.
The scan of the QR code also can provide other information like quality certifications, recipes, and the product’s sustainability profile. In addition, the code opens the door to two-way communication — purchaser to brand owner — by allowing the consumer to give feedback about the product.
Digital platforms also simplify food safety and quality management by automating data collection and analysis. Since issues can be identified more quickly and addressed proactively, produce processors reap numerous benefits. Digital platforms can:
- Yield more sellable product
- Reduce inventory
- Improve food safety
- Increase shipping accuracy and efficiency
- Enhance brand protection
- Simplify regulatory compliance
- Lower testing costs
- Minimize the risk of a recall
- Prevent waste
To further support the visibility and agility needed for traceability, labeling functions are shifting toward digital, frequently cloud-based, platforms where the technology eliminates labeling errors associated with manual processes and simplifies the online integration of printers, coders, cameras, and sensors.
Cloud-based platforms are rapidly gaining share. In fact, the 2022 Gartner technology report predicts, “cloud-native platforms will serve as the foundation for more than 95% of new digital initiatives by 2025 — up from less than 40% in 2021.” (1)
Transitioning to digital technology also will help produce processors comply with the Food Safety Modernization Act (FSMA) section 204, Enhancing Tracking and Tracing of Food and Recordkeeping, and its supporting regulation, final rule on Requirements for Additional Traceability Records for Certain Foods.
The latter is a key component of the FDA’s New Era of Smarter Food Safety blueprint, an initiative the agency announced in July 2020 to enhance traceability, improve predictive analytics, respond more rapidly to outbreaks of foodborne illness, address new business models, reduce contamination of food, and foster the development of stronger food safety cultures.
The requirements specified in the final rule will make it possible for stakeholders to identify and remove potentially contaminated food from the marketplace and thereby minimize the number of foodborne illnesses and/or deaths more quickly. (2)
The final rule establishes traceability recordkeeping requirements, beyond those in existing regulations, for persons who manufacture, process, pack or hold foods included on the Food Traceability List (FTL). With some exceptions, the FTL includes fresh cucumbers, melons, peppers, sprouts, tomatoes, and tropical tree fruits; fresh herbs; fresh and fresh- cut leafy greens; fresh-cut fruits and vegetables; and ready-to-eat deli salads (refrigerated).
Based on a risk-ranking model, the list can be expanded as needed using FDA’s notice and comment rulemaking process. Records for these products must contain Key Data Elements associated with specific Critical Tracking Events and provide information to FDA within 24 hours or a timeframe agreeable to the agency.
The additional recordkeeping requirements apply not only to the foods listed on the FTL but also to products that contain the listed food as an ingredient, if it remains in the same form (e.g., fresh) in which it appears on the list. The final rule is scheduled to take effect on Jan. 20, 2026. (2)
In another effort to reduce foodborne illness, FDA is developing a series of Prevention Strategies to Enhance Food Safety that target specific commodity- hazard pairings. The first three in the series focus on bulb onions, imported enoki and wood ear mushrooms, and infant formula.
During the strategy development process, FDA food safety experts engage with industry, state, international, and other partners to:
- Review outbreak trends associated with certain commodities
- Explore environmental factors that may contribute to contamination in various locations, such as facilities or in more open landscapes like farms
- Review issues related to specific foodborne hazards to identify potential mitigation measures or knowledge gaps
- Review regulations to identify provisions that may be strengthened
- Identify prevention measures that can be taken to reduce future incidences of foodborne illness
- Identify knowledge gaps to expand understanding of food safety issues and limit recurrences of underlying root causes responsible for an outbreak or adverse event (3)
Digital platforms and food safety tactics will be just two of the technologies displayed at PACK EXPO Las Vegas (Sept. 11–13, 2023, Las Vegas Convention Center). For more information, visit packexpolasvegas.com.
1 Gartner, “Gartner Identifies the Top Strategic Technology Trends for 2022,” News Release, Oct. 18, 2021.
2 FDA, “FSMA Final Rule on Requirements for Additional Traceability Records for Certain Foods,” Federal Register, Nov. 21, 2022, p. 70910.
3 FDA, “Prevention Strategies to Enhance Food Safety,” Nov. 15, 2022, Prevention Strategies to Enhance Food Safety | FDA, accessed Feb. 16, 2012.
Jorge Izquierdo is vice president of market development for PMMI, The Association for Packaging and Processing Technologies.