Grading and packing solutions for blueberry packhouses
Changes in the blueberry industry are bringing new challenges to packhouses. There are now pressures to improve both quantity and quality, as well as solutions that make this possible.
According to Joshua Miers-Jones, Global Category director for blueberries at TOMRA Food, demand for fresh blueberries more than doubled in the last decade and is expected to keep on climbing in the foreseeable future at a compound annual growth rate of about 7%. One reason is the transformation of blueberries from a seasonal product to one that’s sold year-round.
Exports are a big driver for sales, which is largely due to production expanding in the Southern Hemisphere. Today, the world’s biggest blueberry exporter (and third-biggest grower) is Peru, followed by Chile and Mexico, with the U.S. fourth in the exporter rankings. This counter-seasonal growing in the Northern and Southern Hemispheres puts blueberries on supermarket shelves every month of the year.
As an integrated line provider for blueberries, TOMRA Food offers solutions for all varieties, fresh to frozen and handling everything from tipping the fruit onto the line to sorting, grading and packing. The company also offers artificial intelligence for increased grading superiority across calyx, stem hole and advanced defect detection.
TOMRA Food’s blueberry solutions are scalable, which make them suitable for small family-owned farms to multinational corporations. And the solutions are modular so packhouse lines can grow as the business grows.
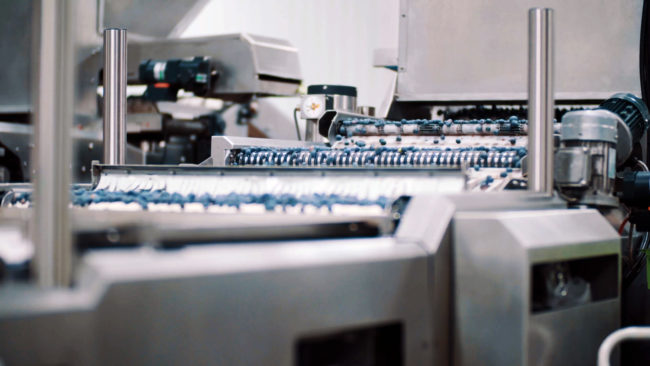
Sorting & grading
TOMRA Food’s precision sorting and grading system for blueberries is the KATO 260. Compact and designed to handle the fruit gently to maximize bloom retention and shelf life, this system is suitable for any fruit sorting condition. Whether sizing fruit into numerous bands or removing defective fruit, the KATO 260 provides five or seven outlets for sorting in any size packing facility.
Fruit is gently loaded onto the KATO260 by an automated Tray Tipper, ensuring a consistent supply and even distribution of blueberries onto the sorter, optimizing throughput. Then the KATO 260’s unique rolling conveyor system singulates and rotates blueberries to allow for a complete 360-degree surface inspection. Cameras take multiple pictures of each piece of fruit, and for precision grading, the machine’s software can identify defects as small as 0.2mm. It can sort at speeds of up to 286 or 572 berries per second.
Case packing
Launched in 2022 is the KETE16 robotic case packing technology. The high-capacity, end-of-line system automates the process of placing punnets and clamshells into cases, trays, boxes and crates. It’s flexible to punnet size, case size and pack orientation, making changing between packs easy.
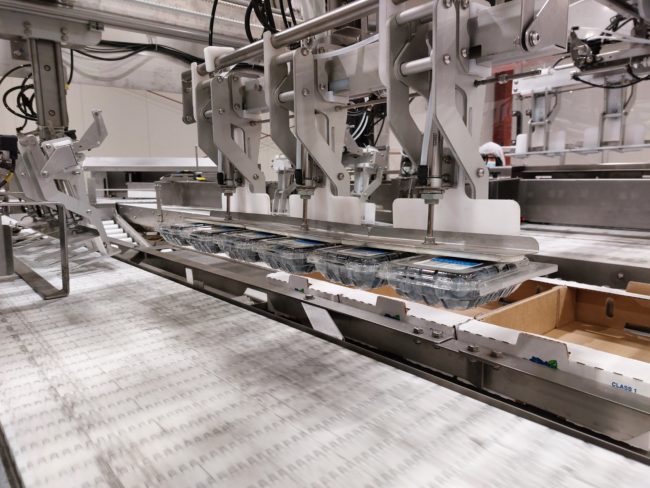
By automatically placing punnets and clamshells into boxes, labor is freed-up from the packing area. Contact points between line workers and the product is eliminated.
The KETE 16 integrates seamlessly to match the speed and capacity of the CURO-16 packing system. The CURO-16 has 16 filling stations, which make it capable of handling up to 200 128-gram packs of fruit per minute. The sorting line’s low drops and minimal transitions ensure the fruit is handled gently as it is directed into packs.
The CURO-8 packing system, with eight filling stations and a smaller footprint is also used by blueberry packers. This packer can handle 110 ppm.