Lone workers: What produce processors need to know
By Dan Smith | Columnist
I think it goes without saying, but the definition of a lone workers still needs to be stated.
“A lone worker is an employee who performs an activity that is carried out in isolation from other workers without close or direct supervision. Such staff may be exposed to risk because there is no one to assist them and so a risk assessment may be required,” as defined by the Health and Safety Executive.
Lone workers in produce processing
Lone workers can exist in many areas of produce processing operations, including all of its supporting operations. There are obvious places to look, but often lone workers is not thought of as working alone.
For example, a high traffic area with workers moving in and out, but the individual job function does not require interaction with the others. There have been instances of warehouse workers not found for hours after being pinned under material or suffering a medical emergency, all while out of sight of other workers traveling in the same area.
A few other obvious lone worker places and activities include maintenance personnel on rooftops, wastewater treatment operators out in the “back 40” and cold storage workers.
Identifying and protecting
Some questions worth answering:
- Do you have a written policy identifying job positions classified as lone workers?
- Do you have seasoned workers, or those with known medical conditions, or at special risk that should carry the lone worker classification?
- Does a lone worker classification require a worn device as standard personal protective equipment?
The Occupational Safety and Health Administration has a “golden umbrella” standard on what’s expected of employers in regard to lone workers. From OSHA’s General Duty Clause.
Each employer (1) shall furnish to each of his employees employment and a place of employment which are free from recognized hazards that are causing or are likely to cause death or serious physical harm to his employees.
When an employer reports an incident to OSHA, the investigation will at some time determine if the employer has satisfied Section 5 (a).
Safety monitoring systems
A worn personal safety monitoring device is designed using accelerometers and timers to sense movement. This will trigger an alarm for an unconscious worker. This device also will provide the worker with a means to manually initiate a panic alarm when injured, immobilized, ill, exposed to imminent threat or any other distress.
Lone worker safety monitoring systems can be summed up into two types.
- A manual check-in system. This system makes it the responsibility of someone to check in with the worker or the worker to check in with someone. This method leaves much room for error. A lot can happen during the time between an expected check in, creating the risk of someone checking out when no one is expecting the check-in. This is simple in concept, but dangerous in practice.
- Monitoring system. This is an immediate notification system having the capacity to notify, identify and locate a worker in distress. These systems may be fee- or subscription-based and supported by cellular technology.
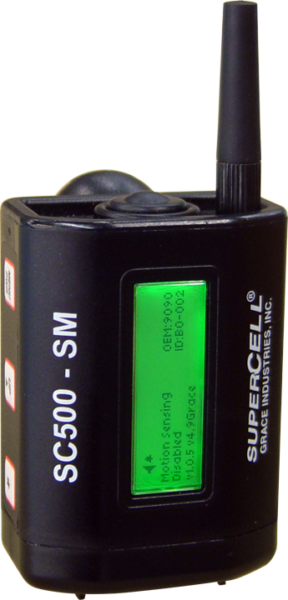
Any lone worker system relying on cellular service should be vetted carefully to ensure that reliable coverage is always available. Any system is only as strong as its weakest link, however.
A cost-effective, non-fee based system uses its own autonomous wireless system specifically designed and tested for use in a workplace.
An effective monitoring system is one that can be used as more than just a lone worker system, but is also capable of integrating with a worker’s present environment. A complete lone worker system should interface with existing alert systems, including fire, weather and active shooter warnings. A complete system also should act as an evacuation system, capable of sending special visual and audible alerts to the worker.
For example, interfacing an ammonia monitor/temperature monitor/pH monitor/flow meter now makes the lone worker system a diagnostic monitoring tool that sends messages to maintenance personnel. It gives them the ability to respond directly from their lone worker monitoring device. A lone worker system can further be used proactively; so that a worker’s alarm triggers an emergency e-stop to shut down a machine or triggers another safety or alerting event.
Expectations
A common misconception is that a system will save everyone. Questions arise like, “How is this system going to protect my worker in the case of a traumatic event?” In this case, common sense will have to prevail. Your lone worker system is only as good as the response plan and response time it takes to render assistance.
Sobering enough, there may be no system or plan that can save the victim of a sudden death. But, if everything is done to plan for providing timely assistance, then you have done everything possible to protect that worker.
When a worker is knocked unconscious or cannot speak, any system relying on voice communication (i.e. two-way radios or cellphones) is essentially useless. The best practice in lone worker system design is one with a defined, engineered and reliable communication path back to the attendant or monitoring authority. A written system testing procedure and regular testing schedule will add comfort in knowing the lone worker system has been tested and operational when needed.
How do you identify and protect your lone workers?
— Dan Smith is director of sales and marketing for Grace Lone Worker.