Cold chain tech companies can aid with supply chain disruption issues
Since early 2020, the global supply chain has been bogged down by seemingly endless challenges, many of which have contributed to labor shortages.
A recent study published by Royal Bank of Canada said 20% of the global container ship fleet is stuck amidst bottlenecks at various major ports. Published May 3, it also said the situation is poised to get worse before it gets better, pointing to China’s COVID-19 lockdown, Russia’s invasion of Ukraine and rising inflation as causes for concern.
For those shipping perishable products, this is not great news. In late January and mid-March, the Biden administration announced plans to ease port congestion. Cold-chain technology provider DeltaTrak has been working on a solution, too. Its real-time, in-transit tracker was designed to address supply chain issues, including delays, missing shipments and damage claims.
USDA announces partnerships to restore disrupted shipping services
In early 2022, exporters were struggling to find shipping containers. Fewer containers were available for agricultural commodities, as ocean carriers bypassed traditional routes to rush containers back to be exported empty. These disruptions were particularly evident at the Port of Oakland, and the ports of Seattle and Tacoma. To address this issue, USDA announced partnerships, first in late January and then in mid-March, to ease port congestion.
Under the first plan, the USDA agreed to partner with the Port of Oakland to set up a 25-acre “pop-up” site to make it easier for agricultural companies to fill empty shipping containers with commodities. They had established a similar partnership in the Port of Savannah and saw significant improvements in the flow of goods. The new site is equipped with a gate that allows shippers to pre-cool refrigerated shipping containers so they can receive perishable goods. The separate loading area should help shippers avoid bottlenecks at the main area of the port.
In mid-March, the USDA announced a second partnership, this time with the Northwest Seaport Alliance. This time they constructed a 49-acre “pop-up” site that, like the Oakland site, is able to receive both dry agricultural products or refrigerated containers. According to the USDA press release announcing the partnership, the Northwest Seaport Alliance had seen a nearly 30% decline in the export of agricultural commodities in the last six months of 2021. What was particularly troubling was that the ratio of loaded versus empty container exports had shifted to predominantly empty containers since May 2021.
The aim of both partnerships is not only to bypass the bottlenecks seen at main port areas, but also to ensure U.S. producers and processors are able to deliver perishable and non-perishable goods to end customers in a timely fashion.
Real-time, in-transit tracking offers extra security
Despite their efforts, bottlenecks still exist, and as the Royal Bank of Canada study points out, it’s only going to get worse. The global supply chain is complex with many check-in points. There are many points along the way where things can go wrong, hindering the delivery of safe, healthy food and creating unnecessary food waste.
Many shippers rely on data loggers, small single-use tracking devices, that monitor time, temperature and humidity, explained DeltaTrak founder and CEO Frederick Wu. In the event of delays or damage, the data on the devices help to support claims. The downside of data loggers is that the data can only be extracted once it reaches its destination. Most data loggers need to be activated at their pick-up location, too. If the shipper forgets to activate it, a claim cannot be made. And since they can only log data, no action can be taken en-route to rectify issues as they develop.
Recognizing these problems, Wu and his team at DeltaTrak set out to develop a better solution, one that would give users more peace of mind.
At the end of March, cold chain technology company DeltaTrak launched its FlashTrak Cloud Service and 4G/5G real-time trackers, as well as its FlashTrak Maritime Service. Both services were demonstrated at Fruit Logistica in Berlin in early April.
DeltaTrak founder and CEO Frederick Wu said the visibility provided by these solutions allows third-party logistics providers, shippers and receivers to deal with supply chain issues such as delays, missing shipments and damage claims quickly and easily.
Wu said COVID put considerable strain on an already complex system, as shippers and receivers couldn’t be there to visibly see what was going on with shipments. With the new real-time monitoring system, though, these challenges are being addressed.
“Now it’s not just after the fact, but you can actually see what is going on right now,” he said.
Having the ability to see shipments in real time offers several benefits, said Wu. First, it allows shippers and receivers to monitor conditions within the container, allowing them to initiate claims before shipments even arrive, if necessary. But it also gives them more flexibility in terms of making corrective actions, preparing for late shipments, and even possibly diverting shipments if ports are blocked or closed.
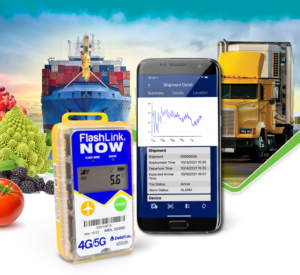
New device models, like the FlashLink NOW 4G/5G Real-Time In-Transit Logger, allow customers to monitor shipment temperature and location, as well as humidity, shock and light. But DeltaTrak took the technology one step further with the development of its FlashTrak Maritime Service, which uses GPS positioning to identify vessel location while on the ocean. DeltaTrak works in partnership with OPTIMIZ Ltd., a claims management company. Working in collaboration speeds up and automates cargo insurance claims.
Erich Hugo, managing director at DeltaTrak, explained how the system works. “If a breach is monitored by one of our sensors — let’s say the temperature profile has been breached — it will immediately create a notification on the dashboard,” he said. “When the customer logs in, it asks them if they want to create a claims notification.”
If the customer says yes, the data is handed over to the claims management company, who can begin to process it right away. The technology has served their clients well. In one case, a customer could see that a container had been left behind in a distribution center near the Panama channel when it was meant to travel further afar with the rest of the containers.
“What’s important is not the fact that our device worked and that the data was correct, but that the customer could make an informed decision based on the data we gave him,” he said.
Real-time tracking has proved beneficial under current challenges as well. As ports in Europe back up due to the Russia-Ukraine conflict, having access to real-time data enables shippers and receivers to find alternate routes or buyers that bypass backlogs.
Going forward, Wu and Hugo believe more claims management companies will come on board once they see the benefits of the device. And as supply chains continue to face challenges, the considerable uncertainty customers face can be somewhat alleviated through more visibility and expedited claims processing.